Attempts at Curved Rail Timelapse Mechanism (9/12/2015)
First a little context:
Years ago, creating a programmable moving platform for timelapse and video was challenging. Most efforts were by photography and electronics enthusiasts. Online communities like the now defunked openmoco gathered user submitted motion control projects. I first discovered platforms like The Chronos Project, miniEngine and eMotimo while loitering around the projects pages and forums. These projects, and others like it have become commercially available as photography, film making and camera motion control becomes more accessible to anyone.
First version of Panning camera platform, 2012
Version 3 of Panning Camera Platform, 2015





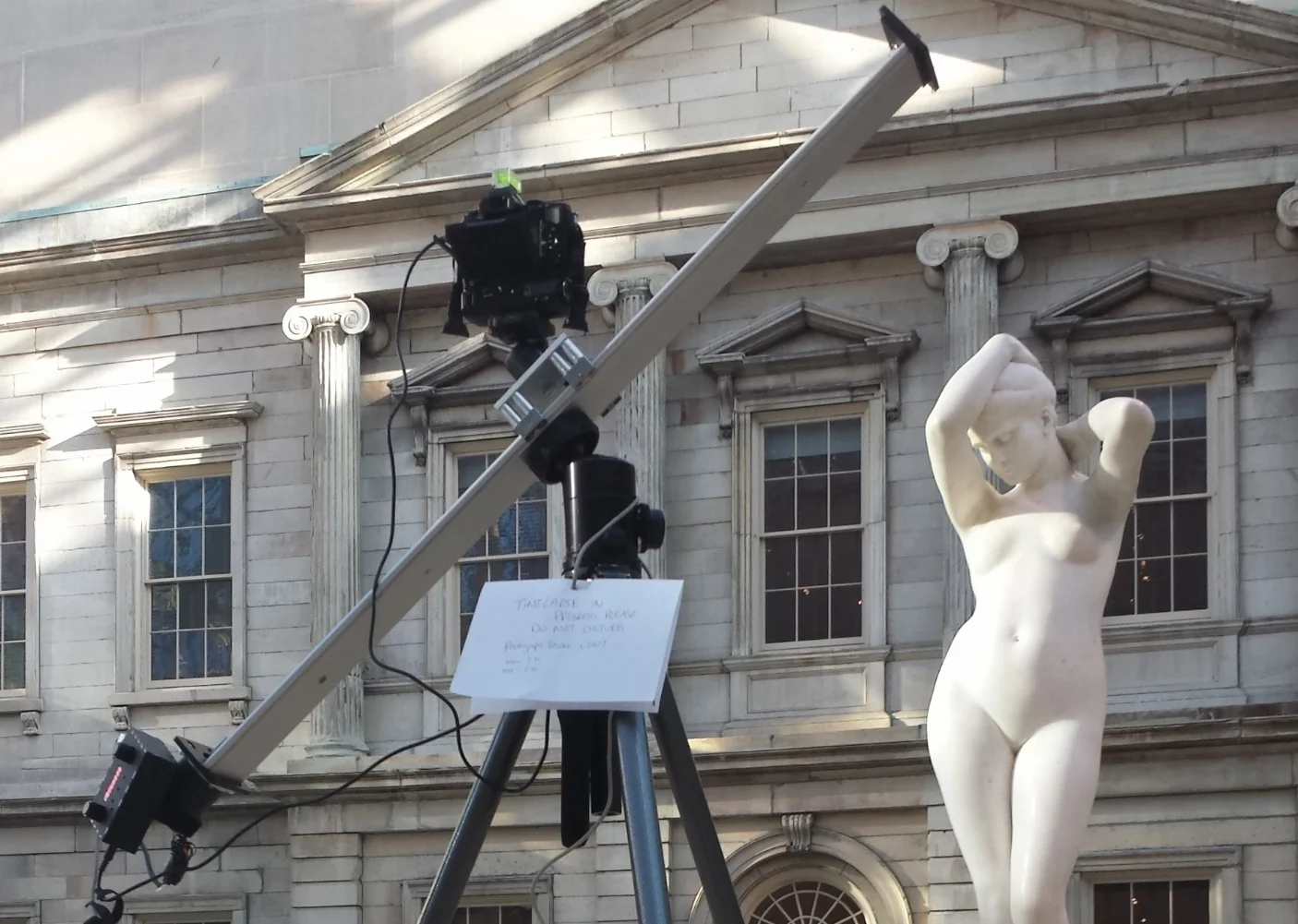
Creating a moving timelapse slider presented many new challenges. Transferring the rotating motion of a motor shaft to the linear movement of a carriage on a rail means customizing existing parts and making up completely new parts. My first attempt at involved alot of hard cutting and shaping of plastic and metal grinding. I used a lead screw to drive the carriage across the rail. It has since been refurbished with 3d printed parts and still works great.
I became interested in adding another axis of movement to the sliding rail. I used two motor controllers (A chronocontroller a miniEngine V1) and a hastily made panning head mated to the slider carriage. It wasn't pretty, but it did the job. Still, adding another movement would be interesting, especially if that movement held a light!
Successful timelapse needs many things, but the most important is the lapsing of time! The trouble is, some indoor scenes and galleries don't give you enough of a sense of time passing. Little to no natural light means shadows don't change much or at all. It's all about the shadows!
I thought adding a curved rail with an LED light could simulate an interesting light movement. even more interesting is the possibility of an orbiting timelapse. Using the curved rail for this kind or automation is difficult. Attempts and solving this problem has lead to frustration and a very messy desk.
It also lead to much on the job training in modelling 3D parts and assemblies.
Internals of pulley. Multiple spools helped maintain tension against the motor pulley.
Spring loaded rail end caps help shift tension while the carriage moved towards it. Ultimately this is where this design failed.
Designing a solution
Initially, I thought of making a large, curving gear rack that followed the shape of the rail. I could simply mount a motor to the side of the carriage, a few gears and done! At the time the gear rack proved difficult to design, and mounting the motor on the side wouldn't allow me to use the entire rail. The next attempt involved pullies, a G2 belt and springs! It didn't exactly work as planned, but who doesn't like pullies and springs!?
After taking some time off, I decided to attempt the original Curved rack gear idea, integrating some lessons learned from the pully failure.
Making a plate to mount the motor at the head of the carriage instead of the side meant it could use the entire length of the rail. Using two gears to reach the curved rack increased torque and allowed the motor to be mounted off of the carriage plate, instead of reaching over it.
The curved rack was still an issue, but I eventually figured out the settings I needed for the size I wanted. The rear rack had to be sliced into pieces small enough to be printed on my machine. Printing gears has been tricky due to the nature of current FFF 3D printing, but I think I've gotten it to a good place.
By designing the parts and assembling them virtually before printing, I'm able to anticipate problems and allow the design to evolve much faster.
For example, I initially designed the gears with a smaller tooth. This worked in the 3D model, but didn't account for the small inconsistencies that happen in the printing process. I decided to redesign the gear teeth to be larger, and to be more forgiving to imperfections in the printing and assembly process.
Larger teeth and post assembly adjustment brace on the carriage allow for fine tuning after printing.
Large Rack gear sliced into 8 pieces for printing.
The large rack gear needed to be sliced up into 8 pieces in order to be printed at home. The gear rack pieces were attached to the rail with JB Weld. The first tests looked promising! The spacing of all the gears were pretty accurate to the 3d models. A little slop is to be expected, but can be addressed with a small adjustments.
Emergency motorized timelapse panning platform!
Panning platform v1 in a DIY Timelapse Rail
While preparing a list of camera equipment to pack on my upcoming honeymoon, I realized I needed (wanted?) some kind of movement for the timelapses I hope to make. At home I use a Igus based lead screw homemade slider controlled by a Chronocontroller (www.thechronosproject.com). I've even made a adapter plate to added panning motion while sliding. These work well enough, but I can't take the slider with me to Hawaii, so I'm settling on a panning base.
The Genie Mini, by Syrp
A few months ago, Syrp announced the Genie Mini . It's a small, self contained panning base for timelapse and video controlled and configured using a phone or tablet! It would be perfect except it's not on sale yet, and won't be available before my trip. There are a few competing products, but non as slick as the Genie mini right now.
While I patiently wait for the Genie Mini to be released, I sketched up some plans for a small panning base I could haphazardly slap together with parts I already have. It will be controlled using the chronocontroller or miniEngine v2 and a 12v battery.
I'd love something small and as flat as possible. Unfortunately, the bulk of the height is taken by the stepper motor. Using the smallest Nema 17 motor I have lying around, the whole base winds up being 65mm high. A bit stout, especially considering it's 85mm diameter. I needed a flat stepper motor! Sincy my timelapse controllers are programmed to use stepper motors, I prefer to design motion around them.
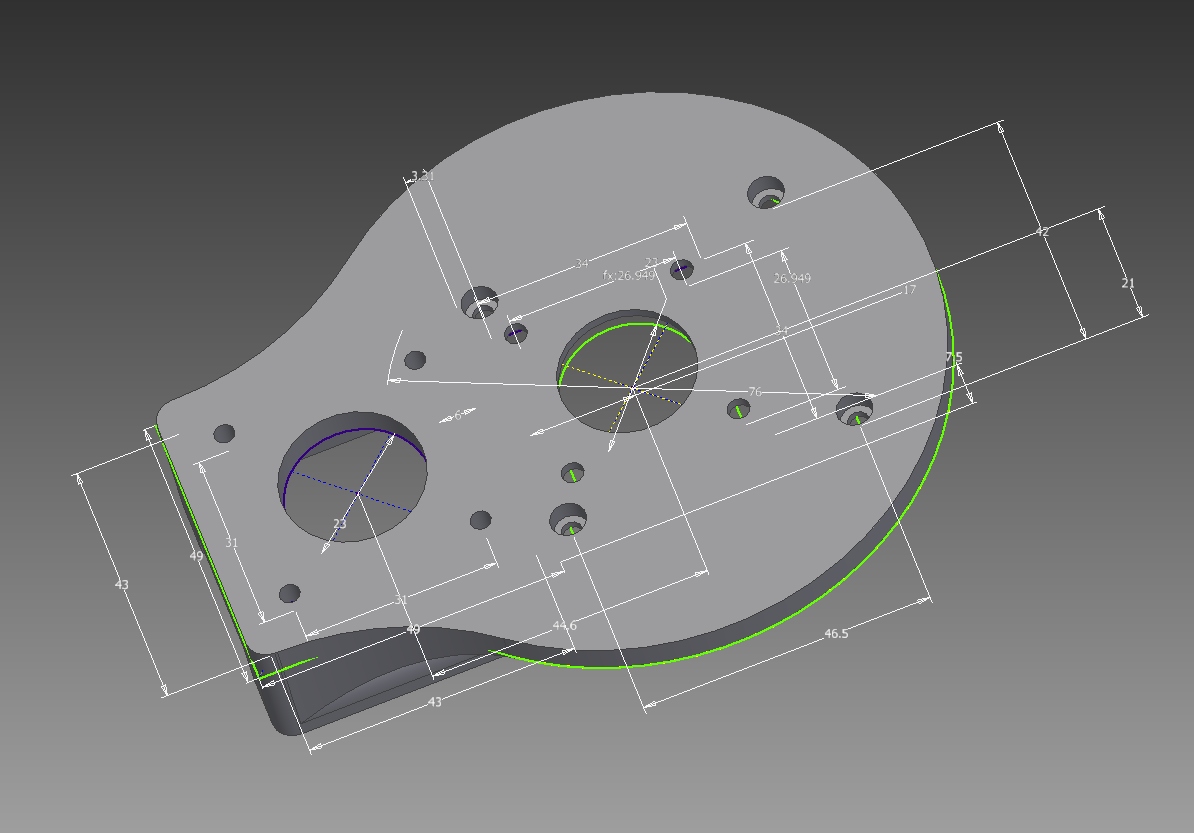

Looking around the internets, I found a Nema 17 "pancake" stepper motor that should work great! A little pricier than most Nema 17 motors, but it's special, and only 18 mm high! Maybe something similar is used in the Genie Mini.
With this fancy pancake stepper, I set out to design something quick and small. It would have to be controlled by my DIY miniEngine v2 box and external battery, or a chronocontroller.
I'd like eventually make this more compact (Hockey puck like) but the next version will have to wait till after this trip. For now, things were looking good! Going even further, I'm thinking making a short slider track I can attach to this base. Might not be sturdy enough for a mirrorless camera, but great for a Go Pro. Stay tuned...
After some printing and tweaks, the final platform was assembled. Still needs a bit of cleanup, but looks good, and works great!
3D printed hand grip for Fujifilm XT-1
Just got a Fuji XT-1 and an loving it! The APS-C sized sensor, 5 analog dials, small size ave great lenses make it a great walk around camera. There are several additional hand grips available for the camera to make it easier to hold. This is especially important for those times when a larger lens is attached. I'll probably invest in the vertical grip eventually, but am on the fence about the hand grip. I thought it would be a good design and print project evoke I'm home sick (cough, sneeze, cough).
I started by finding an image of the bottom of the camera. Using the image as a guide, I drew the bottom of the camera (using Autodesk Inventor) and printed out a small sample to ensure the shape and holes were aligned properly.
A few more revisions, and a good working version is printed.
Will walk around with it for a week and will make more changes if needed!